Servos¶
The user can configure any actuator compatible with the communication interfaces.
Serial¶
Serial servos are configured differently than PWM servos as the protocol of a serial device must be defined with custom messages.
In this case a PWM variable must be sent through a serial interface.
Volz DA26 - RS485¶
Firstly, the following wiring connection is recommended for a RS485 connection between Volz DA26 servos and BCS:
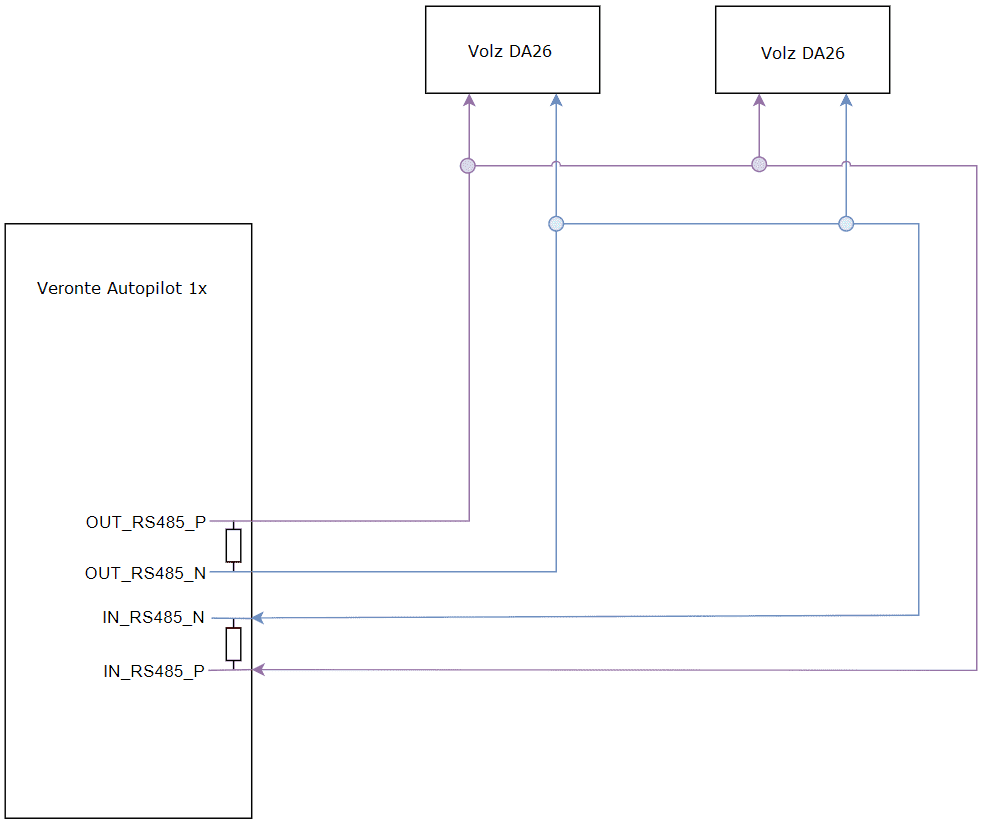
Volz DA26 - BCS wiring connection¶
The above diagram is made for the case where 2 Volz DA26 servos are connected, however, the connection is the same in case the user wants to connect only one or as many servos as the bus allows.
Follow the steps below to configure a Volz DA26 servo via RS-485.
Go to Input/Output menu \(\rightarrow\) I/O Setup section.
Bidirectionally connect the RS485 port to a RS custom message, in this example RS custom message 1 is used:
RS485 \(\leftrightarrow\) RS custom message 1¶
Configure the RS custom message 1 producer by defining the protocol specified by the manufacturer:
Note
As the RS-485 is a Half Full duplex serial port, BCS needs this serial to be free for a certain time in order to receive the servo response. This is done by setting the Delay parameter.
RS custom message 1 - Manufacturer’s communication protocol¶
Endianness: Big endian
Period: 0.035
Delay: 0.0015
Matcher x77: Silent mode command (0x77).
Value: 119
Bits: 8
Mask: 255
Matcher x1: Servo interface Id = 1. The Id will be different for each servo and/or interface.
Value: 1
Bits: 8
Mask: 255
PWM 1: PWM is the variable that carries the information that has to be applied to the servo. Therefore, it must be included in the message.
Variable: PWM 1
Compression: Compress - Bits Unsigned
Encode: 0 / 1
Decode: 3050 / 5070
CRC (Custom): A Checksum is needed to complete the communication protocol.
Type: Polynomial
Bits: 16
Endianness: Mixed endian
CRC - Preset: Custom
BackFrom: 4
BackTo: 0
Polynomial: 32773
Start Value: 65535
Final XOR: 0
Note
For more information on checksum, see Checksum (CRC) explanation of the 1x PDI Builder manual.