Calibrating Servos¶
This section includes the information of how to calibrate the servos that control the attitude of the platform. Configuration of the servos includes: assignment of PWM pins to each servo, controller output to servo output relation, and trimming of the servos.
Servos Output¶
The first step of the process is the servos/actuators configuration. Let´s consider a flying wing as our platform.
The controls in this case are the two control surfaces (elevons) and throttle. Each one of these control variables corresponds to a PWM pin of the connector and they must be positioned in the same order in an S vector representing the Actuator/Servo Outputs.
To assign the actuator outputs go the side panel , click on Setup, then go to Connections
and open the PWM tab.
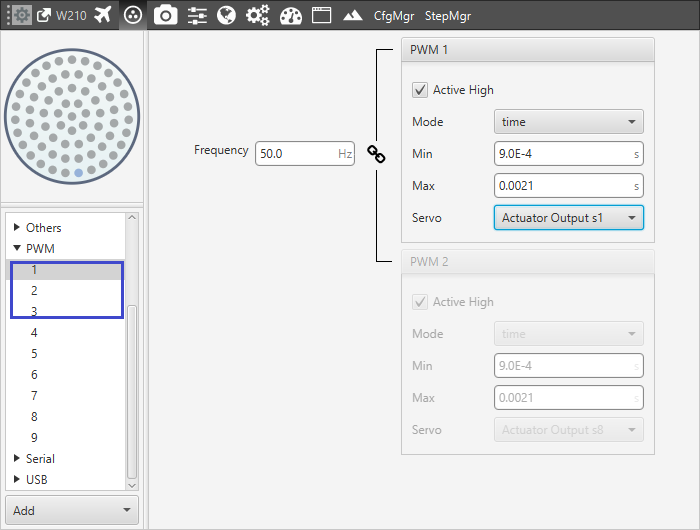
Output-PWM pin links
In this case, only 3 pins are used:
Output 1 – Actuator Output s1 (Elevon 1)
Output 2 – Actuator Output s2 (Elevon 2)
Output 3 – Actuator Output s3 (Throttle)

Output 1 – PWM pin 1 configuration
SU Matrix¶
At this point, the S vector is defined and the SU matrix can be edited. At the Setup menu, go to Devices , then open the Actuators tab, and click on Logical. By clicking on Edit it is possible to configure the relation between the Controller Outputs (U vector) and the servo movements (S vector).
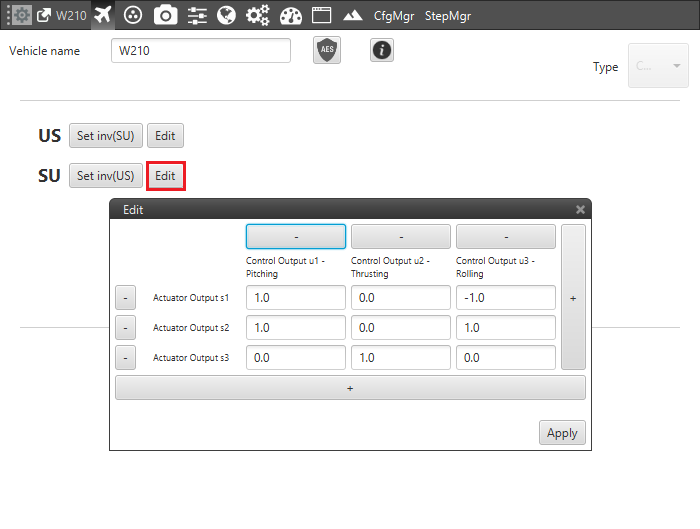
SU matrix editing
A flying wing is configured as follow:
Pitch Control: control surfaces must be moved in the same direction to modify the pitching angle. The contribution of the actuators has same magnitude and direction.
Thrust Control: the Actuator Output 3 is the only one that allows a thrusting change.
Roll Control: in this case, the contribution of the actuators must be set with the same magnit:ref:`Logical <logical>`ude and reverse direction in order to perform a rotation around the body axis of the aircraft.
Warning
The panel above considers the reference system of the aircraft. It should match the Autopilot´s one. In case it would not, it can be edited by clicking on the corresponding axis in order to reverse its direction.
For more information about the logical calibration of the servos check Logical.
System Trim¶
As a final step, the system has to be trimmed. At the Setup menu, go to Devices , then open the Actuators tab, and click on Physical. The options that appear on the screen are presented as follows:
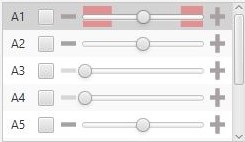
Servos Configuration Display
Servos: this menu contains the servos of the platform. The signal to the system will only be sent if the checkbox next to the servo number (A1, A2…) is marked.
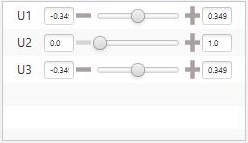
Control Signals Configuration Display
Control Signals: this menu contains the variables (U vector) that represent the control signals generated by the system.
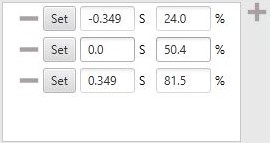
Servo PWM Configuration Display
Servo Position – PWM: this option is used to set the transformation from a control position to a PWM signal. The example above is: a 20º degrees deflection (0.349 rad) of the right elevon corresponds to an 81’5 % pulse to be sent to the corresponding servo.
The other options that appear on the screen are:
To start up: set initial values.
To current value: set the current value.
Change size actuators: change the number of actuators.
Allow command out of limits: allow manual control over the actuators limits established.
Wizard: recommended on first system configuration. It guides the user for configuring actuator limits and performance.
Disable/Enable servos: menu for enabling servos with their limits or just to disable them.
Start up servo position: set the pulse value for the Start up.
Increasing/Decreasing Rate Limit: set a limit for increasing/decreasing value of the servo.
The trim can be performed by moving the servos in three different positions: zero position, minimum and maximum deflection angle (angles are usually limited physically). These positions must be inserted and saved in the software by clicking on Set when the actuator is in the desired position. Otherwise, position can be introduced manually.
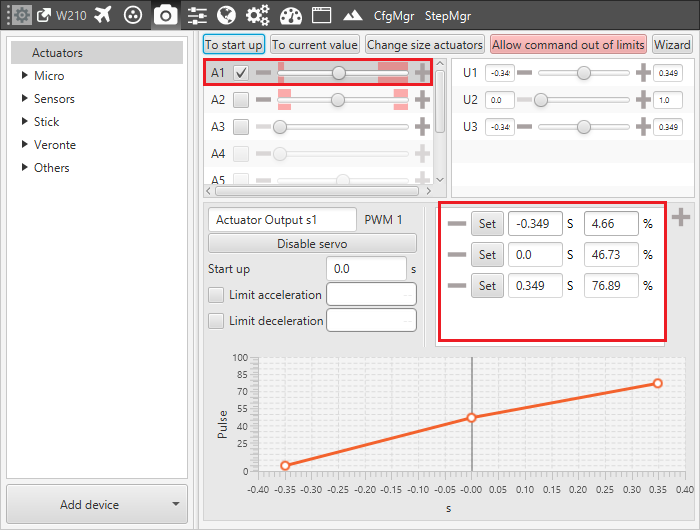
Actuator 1 Trimming
The picture above shows the setting of the elevon number 1:
Minimum: -0.34906 [rad] deflection; 4.66% PWM output.
Zero position: 0.0[rad] deflection; 46.73% PWM output.
Maximum: 0.34906 [rad] deflection; 76.89% PWM output.
Warning
The actuators can be moved directly from Veronte Pipe only when the system is in an Initial phase (when there is no phase selected in Veronte Panel). During the actuator run, if the desired position is in the Out of range zone (red zone), it is possible to click on Allow command out of limits in order to move completely the actuator and find the correct position.
This procedure can be performed in the same way by using the Wizard. This tool allows moving actuators limits easily and finding the correct range, as shonw below.
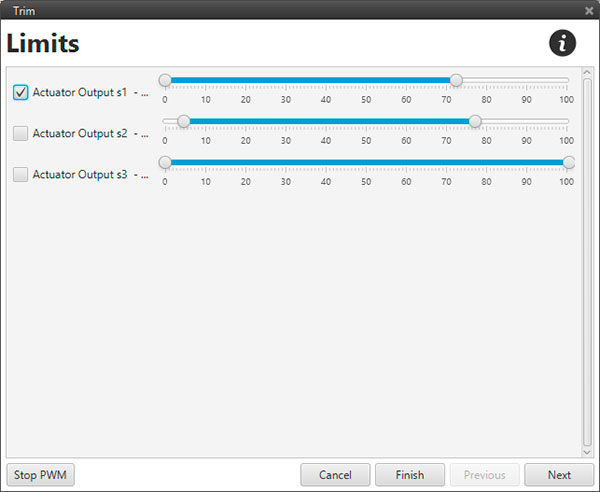
Trim wizard tool
In order to perform a final check, it is possible to select the desired channel and test pitch, roll and thrust control.
The image below shows a pitching output testing. By moving the U1 control, surfaces must change the position according to the reference system: positive corresponds to nose down and negative to nose up.
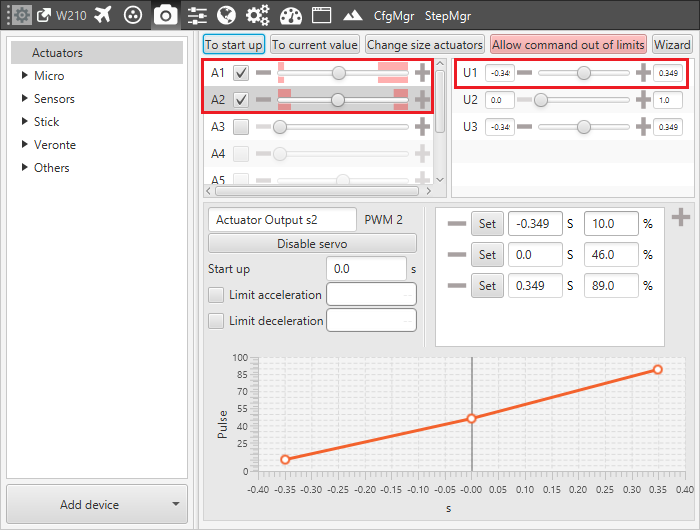
Pitching test
For more information about the physical calibration of the servos check Physical.