Integration examples¶
In this section, a series of examples will be presented so that the user knows how to perform certain customizations in the 1x PDI Builder. In addition, some examples of integration between the Autopilot 1x and external devices are presented.
AP communication with PC¶
Since Veronte Autopilot 1x can be connected to a computer via a USB or serial interface, the configuration for both connections is already set by default in 1x PDI Builder.
However, users should check that this configuration has not been modified to ensure a correct communication via both ways in case one of them is lost. For this:
Go to Input/Output menu \(\rightarrow\) I/O Setup panel. Each USB, RS232 and RS485 Producers must be bidirectionally connected to a Commgr port:
Important
Users should also check that the Commgr ports to which USB and serial ports are connected are not routed. For more information on Routing, see Ports - Communications section of this manual.
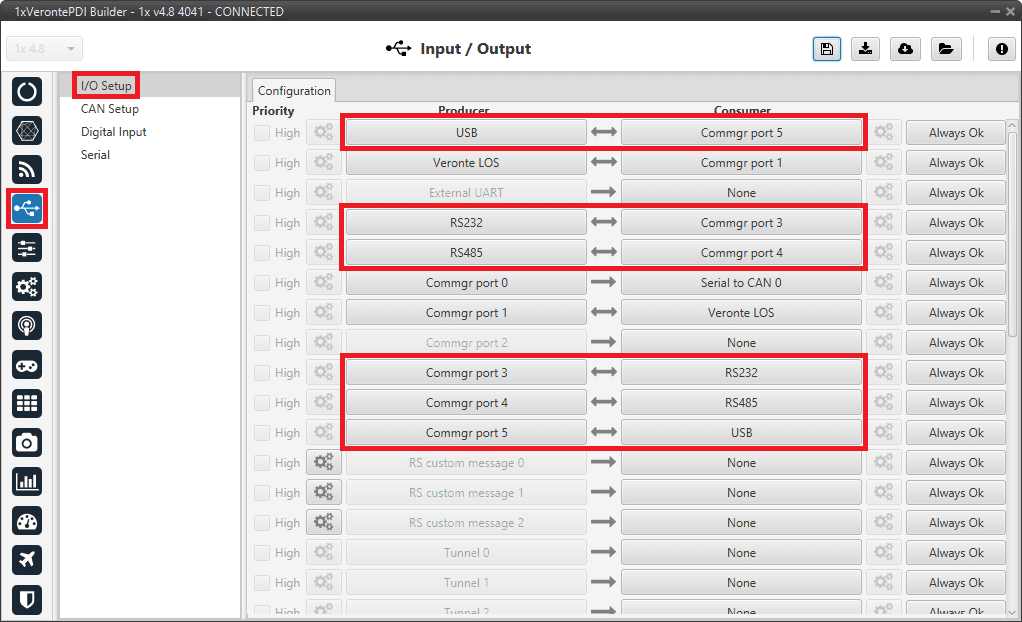
USB/RS232/RS485 \(\leftrightarrow\) Commgr port¶
CAN communication¶
Here are described the steps to be followed in order to correctly receive and transmit CAN messages, both via CAN and serial interfaces.
CAN messages transmission¶
This section summarizes the configuration to be carried out to send CAN streams over a CAN Bus.
CAN messages transmission diagram¶
Go to Input/Output menu \(\rightarrow\) CAN Setup panel \(\rightarrow\) Custom message 0 tab.
Select the fields to send in TX or TX Ini, as it is a Producer. More information on the configuration of CAN messages can be found in the TX/TX Ini Messages (Custom Messages) - Input/Output section of this manual.
For example, a CAN message set to ID 12:
CAN messages transmission - Custom message configuration¶
Go to Input/Output menu \(\rightarrow\) CAN Setup panel \(\rightarrow\) Configuration tab.
Connect CAN custom message 0 producer (as the message has been configured in the Custom Message 0 tab) to an Output filter as follows:
CAN messages transmission - CAN Setup configuration¶
Warning
Remember that it is necessary to have at least 1 free mailbox for TX messages.
CAN messages reception¶
This section summarizes the configuration to be carried out to receive CAN streams over a CAN Bus.
CAN messages reception diagram¶
Go to Input/Output menu \(\rightarrow\) CAN Setup panel \(\rightarrow\) Mailboxes tab.
Configure the mailbox to receive a message with the appropiate ID (in this example ID 28 has been configured):
CAN messages reception - Mailboxes configuration¶
Go to Input/Output menu \(\rightarrow\) CAN Setup panel \(\rightarrow\) Configuration tab.
Connect an Input filter with the right CAN ID to a Custom message consumer:
CAN messages reception - CAN Setup configuration¶
CAN messages reception - Input filter configuration¶
Go to Input/Output menu \(\rightarrow\) CAN Setup panel \(\rightarrow\) Custom message 0 tab (as Custom Message 0 has been selected as consumer).
Configure the message reading as desired in RX by setting the correct CAN ID.
The different options and parameters to be configured are explained in the RX Messages (Custom Messages) - Input/Output section of this manual.
CAN messages reception - Custom message configuration¶
CAN messages transmission via serial¶
This section summarizes the configuration to be carried out to send CAN streams over a serial Bus.
Note
For sending CAN streams over a serial bus, a CAN wrapper port is needed. For further details of this port, please consult the CAN wrapper/CAN unwrapper - I/O Setup section of the present manual.
CAN messages transmission via serial diagram¶
Go to Input/Output menu \(\rightarrow\) CAN Setup panel \(\rightarrow\) Custom message 0 tab.
Important
The index of the Custom message tab must match the index of the CAN custom message producer to configure. In this example, tab 0 is selected.
Select the fields to send in TX or TX Ini, as it is for transmission. More information on the configuration of CAN messages can be found in the TX/TX Ini Messages (Custom Messages) - Input/Output section of this manual.
For example, a CAN message set to ID 12:
CAN messages transmission via serial - Custom message configuration¶
Go to Input/Output menu \(\rightarrow\) CAN Setup panel \(\rightarrow\) Configuration tab.
Connect CAN custom message 0 producer (as the message has been configured in the Custom message 0 tab) to a CAN wrapper consumer as follows:
CAN messages transmission via serial - CAN Setup configuration¶
Go to Input/Output menu \(\rightarrow\) I/O Setup panel \(\rightarrow\) Configuration tab.
Connect the CAN wrapper 0 producer to a RS232 or RS485 consumer as shown below.
Important
The index of the CAN wrapper producer must match the index of the CAN wrapper consumer configured in the previous step.
CAN messages transmission via serial - I/O Setup configuration¶
Warning
Remember that it is necessary to have at least 1 free mailbox for TX messages.
CAN messages reception via serial¶
This section summarizes the configuration to be carried out to receive CAN streams over a serial Bus.
Note
For receiving CAN streams over a serial bus, a CAN unwrapper port is needed. For further details of this port, please consult the CAN wrapper/CAN unwrapper - I/O Setup section of the present manual.
CAN messages reception via serial diagram¶
Go to Input/Output menu \(\rightarrow\) I/O Setup panel \(\rightarrow\) Configuration tab.
Connect a RS232/RS485 producer to a CAN unwrapper consumer.
CAN messages reception via serial - I/O Setup configuration¶
Go to Input/Output menu \(\rightarrow\) CAN Setup panel \(\rightarrow\) Mailboxes tab.
Configure the mailbox to receive a message with the appropiate ID (in this example ID 28 has been configured):
CAN messages reception via serial - Mailboxes configuration¶
Go to Input/Output menu \(\rightarrow\) CAN Setup panel \(\rightarrow\) Configuration tab.
Connect a CAN unwrapper producer to a Custom message consumer. In this example, Custom message 0 consumer is selected.
Important
The index of the CAN unwrapper producer must match the index of the CAN unwrapper consumer configured in the previous step.
CAN messages reception via serial - CAN Setup configuration¶
Go to Input/Output menu \(\rightarrow\) CAN Setup panel \(\rightarrow\) Custom message 0 tab.
Important
The index of the Custom message tab must match the index of the Custom message consumer to configure. In this example, tab 0 is selected.
Configure the message reading as desired in RX by setting the correct CAN ID.
The different options and parameters to be configured are explained in the RX Messages (Custom Messages) - Input/Output section of this manual.
CAN messages reception via serial - Custom message configuration¶
Data transmission between Veronte Autopilots 1x¶
To establish a proper communication between the ground and air units, the telemetry and sniffer menus must be configured, respectively.
A simple example of use between a ground unit and an air unit is shown below:
In the 1x ground unit:
Go to Telemetry menu \(\rightarrow\) Telemetry panel \(\rightarrow\) Data link to VApp tab (for more information about this, see Data vectors - Telemetry section of this manual).
Add the variables: Absolute: UAV position, Yaw, Pitch and Roll.
Set a Frequency, it is recommended to set it to 10 Hz.
On Address, point to the 1x air unit (it is needed to have both units connected through the radio in order to be able to see them on the menu).
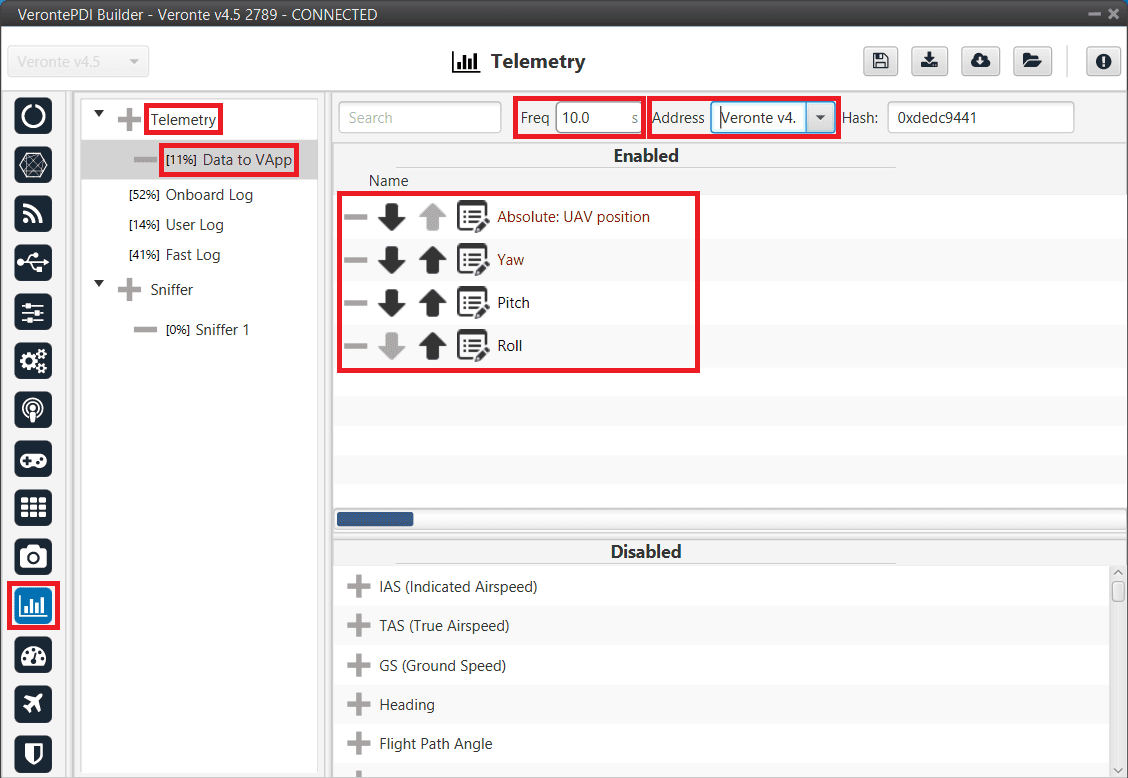
1x ground unit - Telemetry¶
For the 1x air unit:
Go to Telemetry menu \(\rightarrow\) Sniffer panel (for more information about this, see Sniffer - Telemetry section of this manual).
Add a new Sniffer.
Configure the same variables (keeping the same order) than in the ground unit.
On Address, point to the 1x ground unit.
In the gear next to it, configure the 4 incoming variables as System Variables: assign UAV Position to Moving Object and the 3 variables from attitude to 3 different User Variables (keeping the same order as well).
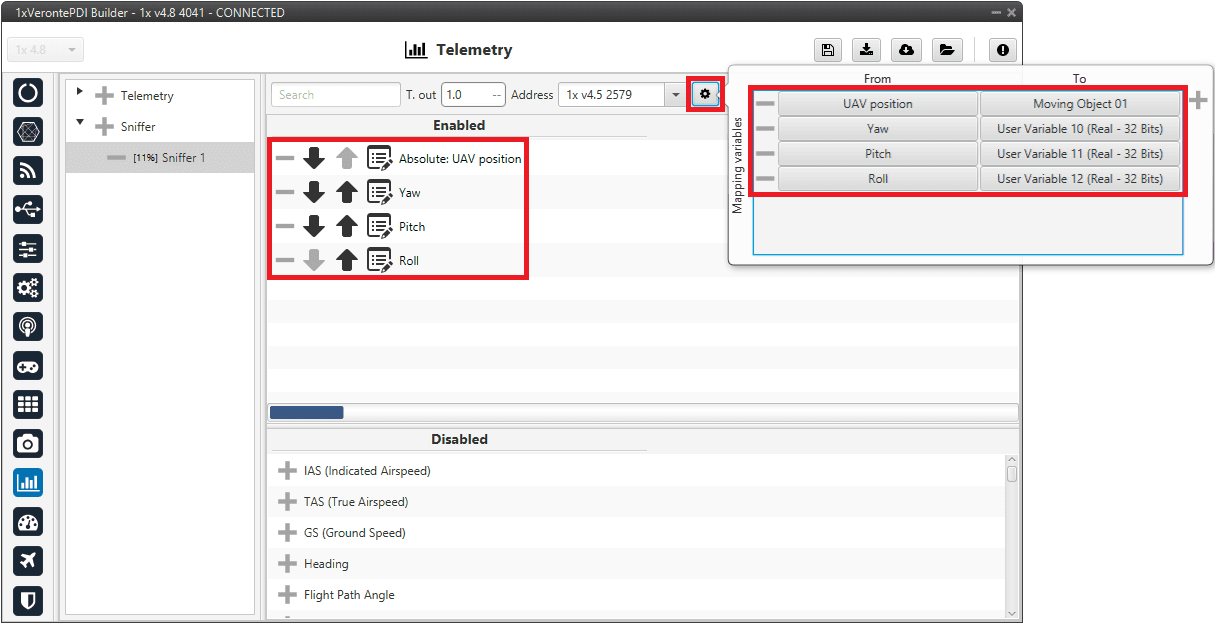
1x air unit - Sniffer¶
Flare and Decrab phase configuration¶
As flare and decrab guidance are not included in the landing algorithm, since the decrab is control dependent (yaw must be aligned with the runway direction), the following shows how to implement this guidance in a generic fixed wing configuration:
First, it can be useful to create a program that computes the altitude above the touchpoint, the lateral error over the desired route and the heading error. If all conditions met, the flare phase is triggered:
Flare and Decrab phase - Auxiliary program¶
Flare and Decrab guidance definition
In the Guidance program (where the guidances for all phases are defined), add the Flare phase to the Phase Switch block. Then, the flare and decrab guidance must be built as follows:
The desired vertical speed is overwritten to be a function of the height above the runway. In this case the height is calculated in an auxiliary program (Height Above Touchpoint variable calculated in step 1), but the AGL could be used.
The desired yaw is overwritten directly by the runway direction.
The desired roll is overwritten to 0º.
The desired IAS is overwritten to a speed slightly above the stall speed, in this example 15 m/s.
Flare and Decrab phase - Flare and decrab guidance definition¶
Pitching control
The desired vertical speed is used for pitch control as shown below:
Flare and Decrab phase - Pitching control¶
Thrusting control
The throttle is used to maintain the IAS (slightly above stall) and when a height above touchpoint of 1 m is reached, the motor is cut off. Again, a user variable is used here (Height Above Touchpoint variable calculated in step 1), but the AGL could be used:
Flare and Decrab phase - Thrusting control¶
Rolling control
For the roll, simply try to maintain the desired roll (0º):
Flare and Decrab phase - Rolling control¶
Yawing control
The yaw control (rudder) is based on the desired yaw:
Flare and Decrab phase - Yawing control¶
Important
This algorithm requires a good yaw estimation if users want to have Decrab, so magnetometer or GNSS Compass is required.
Flare phase configuration¶
However, for a Flare phase without Decrab, the yaw control should be based on heading instead of being based on yaw. To do so, the Guidance and Yawing programs must look as shown below:
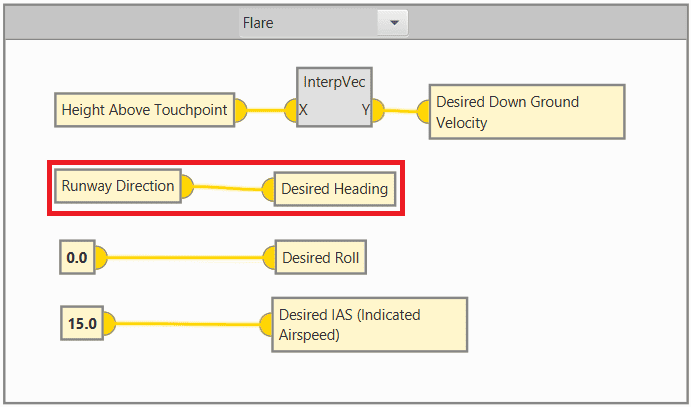
Flare phase - Flare guidance definition¶
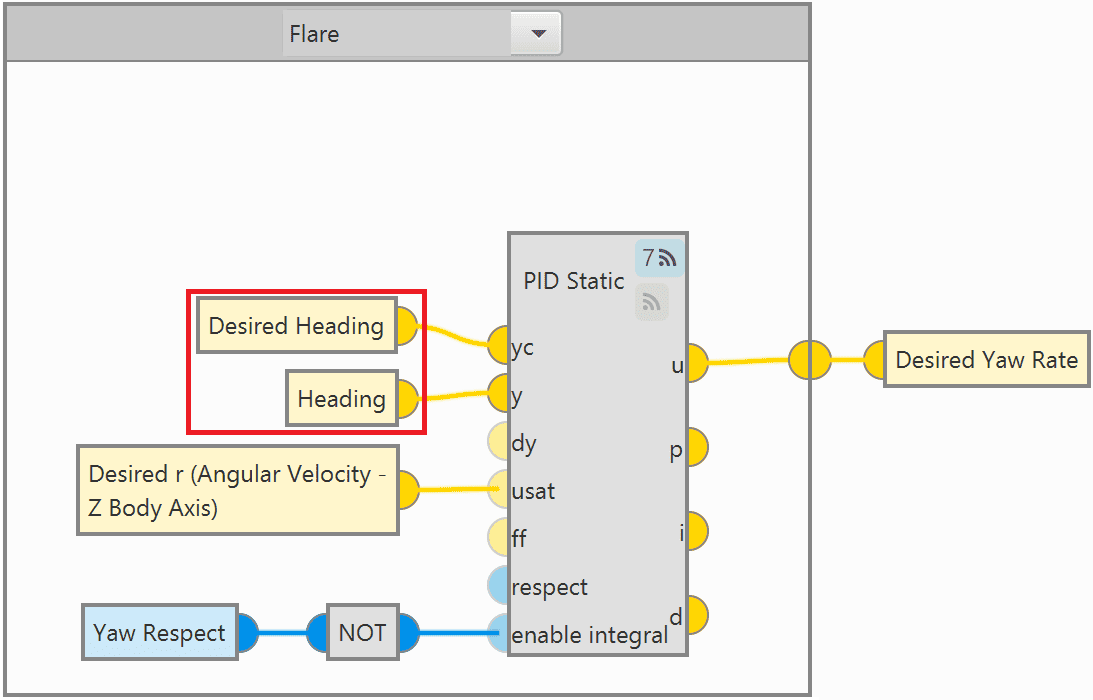
Flare phase - Yawing control¶
For more information on block programs, please refer to Block Programs section of this manual.
RTK Configuration¶
The RTK configuration is performed through the GNSS sensor block with the help of the RTK Wizard.
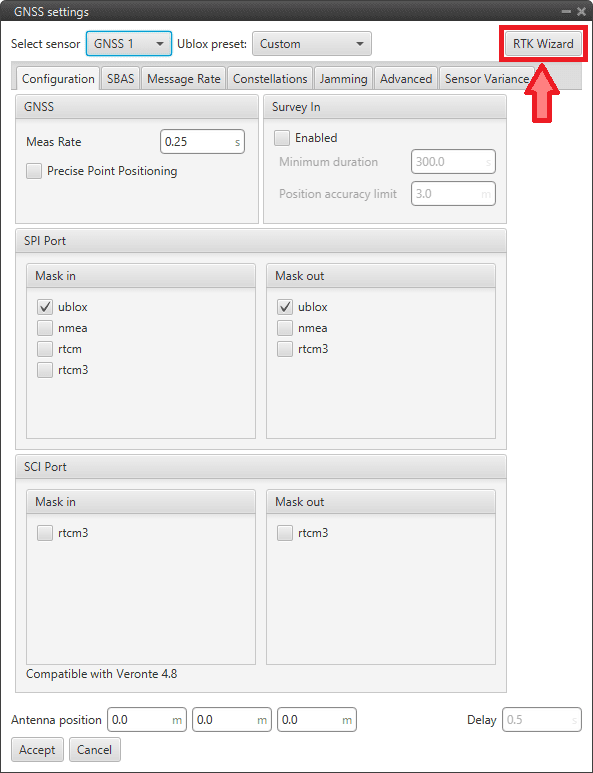
RTK Configuration - GNSS block¶
Users must use this wizard to perfom the corresponding settings for the 1x air and ground units:
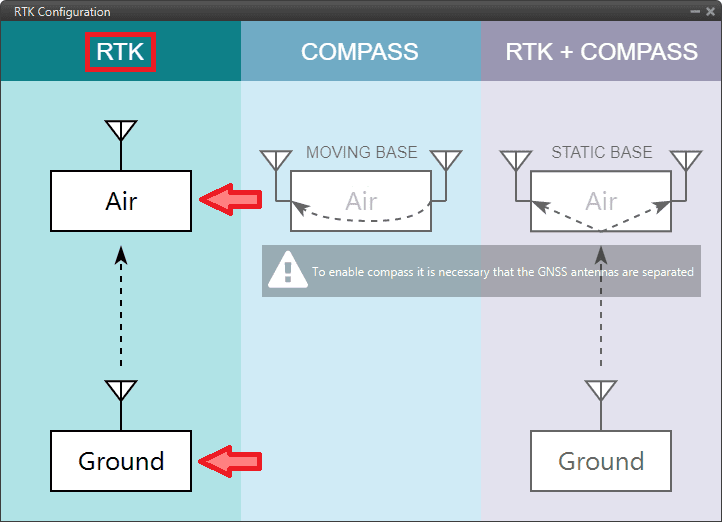
RTK Configuration - RTK Wizard¶
Danger
This wizard uses by default the Y0 splitter port. Consequently, if it has been configured for another use, the configuration will be now overwritten.
Therefore, to avoid system malfunction when using RTK, it is highly recommended to leave the Y0 splitter on the ground unit “free”.
This is especially important if the ground unit is a PCS.
For the 1x air unit, click on “Air” in the RTK column and the corresponding RTK configuration will be automatically applied to the user’s configuration.
For the ground unit, click on “Ground” in the RTK column and the corresponding RTK configuration will be automatically applied to the user’s configuration.
In the Ublox preset parameter, the Static base option will be selected. However, if user wishes to consult the configuration made, just select the Custom option:
RTK Configuration - GNSS block ground configuration¶
Important
Please pay specific attention to the “survey configuration” options.
For a detailed explained of the GNSS sensor block, please refer to GNSS sensor - Sensors blocks of Block Programs section.
With the previous configurations, when GNSS accuracy < 3 m \(\Rightarrow\) GNSS sensor will start the survey in during 300 seconds while taking measurements for RTK correction.
To verify correct survey in behavior, in Veronte Ops users can query the status of the following variables.
In the ground unit, if the survey in has started, ‘GNSS1 Survey In Off’ bit should be in “success” mode \(\Rightarrow\) GNSS1 Survey In (if the label has the default setting, it will be green).
Therefore, when finished, the bit will switch to “fail” mode \(\Rightarrow\) GNSS1 Survey In Off (if the label has the default setting, it will be colored red).
On the 1x air unit, once the survey in has finished, check that ‘DGNSS1 Input Off’ and ‘DGNSS1 Navigation Off’ bits are in “success” mode \(\Rightarrow\) DGNSS1 Input On and DGNSS1 Navigation On respectively (if the labels have the default setting, they will be colored green).
At this time, the GNSS1 Accuracy value in the air unit, should be very low, probably between 0.01-0.05 m.
External devices¶
The step-by-step instructions for the following external devices will be explained in detail in the following sections: